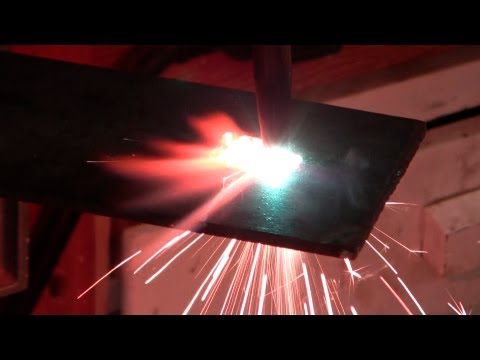
This video shows part I of how I diagnosed and replaced the AC compressor clutch pulley bearing from the air conditioning compressor on a 5.9L 1998 Dodge Ram…
This video shows part I of how I diagnosed and replaced the AC compressor clutch pulley bearing from the air conditioning compressor on a 5.9L 1998 Dodge Ram…
You must be logged in to post a comment.
I’ll throw a total guess at $300, but I could be way off. Many mechanics would replace the compressor, and when you open the system to do that there is lots more to do. When the system is opened, good standard care is to also flush the system, replace the receiver/dryer, replace all seals, and do a vacuum test. I will guess that the later may be in the $1500 range, but again I could be way off. Newer vehicles have very difficult access to the compressor so cost for repair goes way up….
OK, when i take it to the machanic, how much is a fair cost to repair? If he does what you have done? by the way….thanks so much!
I hope it works as well for you as it did for me. Good luck!
Great video. I have the exact problem and this will be a great help in fixing it.
Thanks for the update, I’m glad it worked out for you.
Update, you know i bought a remanufactured compressor online for 99.00 shipped so i went that route, i found the compressor bone dry so i drained the old oil from the new comp. added about 5 oz oil and installed, no growling, it’s a winter vehicle so not really interested about the A/C working but i could fix — i returned the old bearing for 25.00 refund
Good thinking. I have three of those wrenches, including an adjustable one. I tried all three before I made my own. Good luck with your repair!
I had a short in my wires that went into the compressor, a simple splice and the compressor started cycling again.
Thanks for the video, I found a wrench from my angle grinder worked perfectly to get the clutch plate loose, much easier than fabricating one of my own.
Yes, i was watching things to that effect but i don’t have any equipment– i know about replacing all the o-rings, i will look into the dryer and also find out who will do the entire charge including the vacuum, etc. It’s possible i don’t have a leak but just that it hasn’t been recharged in ages as it’s a 96. To be honest since the system was empty it’s quicker just to replace the compressor than do the bearing, i think in the long run probably better to replace the compressor anyway —
Good luck, too bad a simple repair didn’t work for you. Remember to flush the system, replace the receiver dryer, replace all O-rings and clean the expansion valve or orifice tube, then vacuum the system down to remove all water and check for leaks.Calculations for oil and freon are tricky without the right equipment.
I just removed the compressor and got the bolt out, the A/C didn’t work so i just doubled checked the low pressure side– it appears that the clutch is permanently attached to the pulley via 3 pins so even if i get the pulley off not sure how i can get the bearing out? Not worth the aggravation- I am just going to replace the compressor, ebay has for $100.00 and return the new bearing which was was $35.00 My clutch never engaged , possibly because of being empty so i’ll start from square one
You might do a video to help others in the same situation, pay it forward, ha ha.
Thanks, i just looked at my 96 ZJ as i recently received the new bearing and there aren’t 3 holes like yours, just a recessed center bolt, it’s not a nut so Chrysler must have changed it– The bolt also has a small head so most likely it’s small and fragile — I think i will spray then try to loosen with belt and compressor in place to hold pressure on the pulley
It’s shown in the video at 10:10, using a press. You don’t need a press, you could use a hammer and a socket and a block of wood, as long as the metal flange is supported well.
Sometimes in Youtube, videos are truncated to a shorter length than originally posted. Maybe that happened when you viewed. To see the whole video, hit refresh or reload, or access the page again — the whole of part I should be 11:26 long. Thank you for watching.
Yeah, I think most people would find that an impact is all that is needed. Thanks for watching.
Thanks you very much, your video was really help full. I used a impact drill to remove the front nut? I was turning fast without turning the compressor so no need of special tool. Tanks Pascal, Quebec, Canada
I’m just wondering how you got the berrings out of the original clutch pully cause in the video it looks like its skips that part
It’s cool to meet people like you, who find their own solutions without a lot of expensive tools. In my case the nut wasn’t on all that tight, but my weak air tools weren’t able to twist it off. Good luck!
Great video, i have a 96 Jeep Grand Cherokee with the 5.2 and am going to replace my bearing very similar parts involved, i didn’t know i needed a spanner wrench or puller but i previously mad a spanner wrench for the water pump from a bicycle pedal wrench so i can just drill another hole
I hope it works for you, mine is still running fine. You might improve this thread if you were to post a followup comment, to say how it went for you.
You’re welcome, it was a fun video to make.
Thank you!
If I have time tomorrow I”ll measure it for you. It was just trial and error to get the right size.
I’m glad it worked, thanks for the followup.
Fantastic. Last week had my truck camper on & pulling a boat when the bearing went out. Like you said, I could not find parts without buying the whole compressor assembly. Made my own tool by drilling holes in an old tube bender handle. Didn’t have a torch, so cut a half round groove with bench grinder for socket clearance. Used a 6 inch c-clamp to press in & out. I was about to bring it in the shop until I saw your videos Thanks again as it is also hot in Minnesota.
Great video thanks what size belt did u have to get to bypass the compressor?
Same compressor on a 2006 i9200 International bigRig and thanks for the insight as I am having a hell of a time getting the clutch pulley off.
I’ve heard it said that some snap rings have a ‘side’, so even though mine didn’t I suppose it is possible to put it in wrong. In any case, that’s worth checking. Also check to be sure the coil is sitting properly in that little notch so it can’t spin and hold everything out a little too far. I would check the clearance of your clutch plate to be sure it is right. Mine had a little wobble too, but it is better now. When stuff like this happens to me I take a break and look for obvious things.
I can spin it like you did with a socket. the pulley seems to have a slight wobble to it.and the clutch plate is scrubbing on one side against the pulley. I checked for oil leakage behind the coil its good.also the snap ring on the pulley is on but looks like its on better on the front than the back? if that is even possible? it worked fine before I pulled the pulley off, all except the bearing. but the compressor and clutch did fine.there wouldn’t be a way to rig it in a always on would they?
Maybe your compressor is failing, causing too much resistance. I hope not. Can you spin the compressor easily by hand?
ok I replaced the pulley bearing and got it ask assembled back together. but now the clutch plate is slipping. half the time it engages. and half the time it just spins but slips bad enough to make the compressor not work and cool. i’ve tried adding and removing shims but nothing seems to help. please help me it’s hot !
The coil comes off in about a minute – it’s easy to get off. You don’t have to do much with it as long as it hasn’t overheated and fried. You can’t really see the seal until the coil is off. If the bearing is failing, you don’t want to be stranded on a long trip, like I was. And when the pulley overheats it does heat damage to surrounding structures. So, if I knew the pulley was failing I would fix it now. In the meantime I would have a backup roadside plan in case it failed suddenly.
So if I can get the clutch plate off and then the pulley. I should be able to replace the bearing without messing with the coil, correct ? I know my compressor could be leaking but I may be able to tell that with the coil still installed. Or if it works now {which it does} I can just keep letting it work until the compressor fails, And then just replace it. So I might as well just let it keep working as long as it will right ? I’m sure the pulley bearing is dying though, but not seized yet.
Thankyou, Bob, for your contribution to this thread. Like you say, there are many ways this problem can be approached and you have outlined another successful option.
I have a string of other videos planned for this vehicle, some of which are almost finished. However my A/C problems seem to be solved so far. Cheers,
Dave